PCBs for Power/Energy Applications
Our planet is currently faced with the significant challenge of escalating climate change. In the realm of power and energy, we recognize the pivotal role in addressing this challenge. The industry is in the midst of a profound transformation, transitioning from fossil fuels to alternative and decentralized energy sources. This transformation, while complex, involves navigating new regulations and harmonizing both traditional and modern approaches.
Below, you will find a selection of applications we offer, designed to actively contribute to the transition towards sustainable and climate-conscious power and energy solutions.
- Battery Management Systems: PCBs for management of mobile battery systems. Demands are thermal management, long lifespan and size constraints due to power density.
- Energy Storage Systems: PCBs for battery/thermal management and control systems. Demands are thermal management, long lifespan and size constraints due to power density.
- Multi-Layer | Flex | HDI | Heavy Copper
- High Voltage Control: PCBs for measurement and control in high voltage environments. Demands are isolation distances, controlled stack-ups and mission critical function.
- High Voltage Isolation Management: PCBs for high voltage protection surveillance. Demands are high voltage isolation (air gap) and long service life in harsh environments.
- Mixed Energy Management Systems: PCBs for power conversion, management and control. Demands are thermal management, long lifespan and size constraints due to power density.
- Multi-Layer | Flex | HDI | Heavy Copper
- Power Factor Correctors: PCBs for PFC-units (power factor correctors), within building or industrial drives with large AC-consumers like AC-motors, etc. Demands are typically long lifespan and durable design.
- Transformer Management: PCBs for transformer control, performance management and protection. Demands are high voltage isolation (air gap) and long service life in harsh environments.
- Voltage Converters: PCBs for solar panel parks, windmills or battery. Demands are heat management and long lifespan. Battery management systems often have demands for a high-density design as well.
We are an ISO 9001:2015 certified PCB supplier that can support your most intricate power/energy circuit board designs.
Give us a try for your Power & Energy needs!
Printed Circuit Boards for High-Current Applications
Printed circuit boards, or PCBs, are crucial elements for industries that rely on high-current applications. These solutions, especially heavy copper PCBs, can withstand high currents as well as loads of mechanical stress.
Millennium Circuits Limited has a range of high-power PCB solutions to support your applications, whether you operate in the automotive or industrial equipment industries or with medical instruments or marine technology. With our innovative solutions and exceptional hands-on support services, we’re here to help grow your high-current operations.
Design Considerations for High-Power PCBs
Standards for high-voltage PCBs are stringent. But with the correct materials and design, a high-voltage PCB will be functional and safe. Here are a few things to consider for your high-power PCB design.
- Airflow
- Amount of power
- Board material
- Temperature
- Vias
The amount of airflow around your circuit board is crucial, as it also relates to temperature and the possibility of overheating. The heat generated from the device’s circuit must dissipate into the cooler air around it. If the heat gets trapped, it can create a hot box and cause your PCB to overheat.
One of the most vital components in designing a high-power PCB is knowing the power path. Knowing the amount of power and its location will help you understand the integrated circuit’s position and the type and amount of dissipated heat required on the PCB. Power can affect many aspects of the circuit board design, such as board material, ambient temperature, airflow around the board and integrated circuit density.
Temperature is another crucial element in your PCB’s design. Because high temperatures can result in permanent damage or malfunctions in your board, you’ll want to understand common causes of high heat in PCBs, how to prevent it and how much heat a PCB can withstand. Common causes of high temperatures range from through-hole interference and high-frequency circuits to lead-free solder processes, surface-mount device distance and component malfunction.
You can prevent high temperature levels in your circuit boards by implementing solutions such as heat sinks, fans and laminates. Other ways include integrating heat pipes, increasing the PCB plate thickness or maintaining spacing. Your high-current PCB’s material will determine how much heat it can withstand. For example, a copper plate with optimal thermal components can resist high temperatures, while other materials are less reliable.
Vias help transfer heat and power from the electronic components to an exterior heat sink while also carrying higher currents through the PCB. Also called heat vias, these components are the connection between the board and the heat sink. Copper plating within vias reduces the design’s thermal resistance.
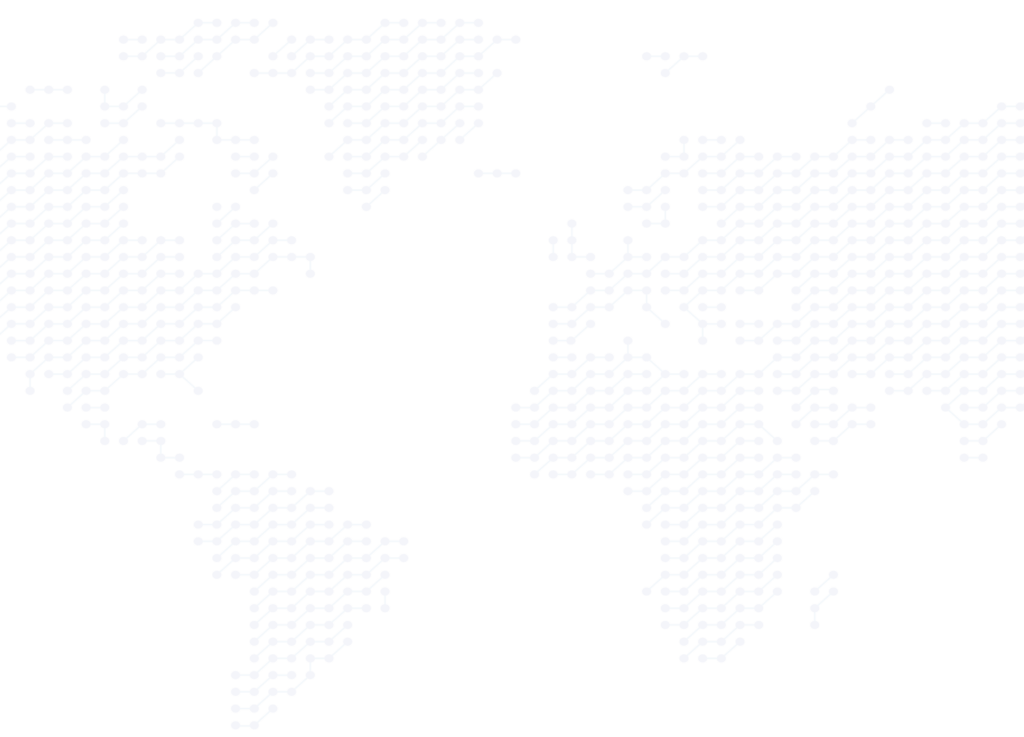
Challenges of High-Current PCBs
High-current printed circuit boards are impressive devices that can withstand many elements other boards can’t. However, they come with several challenges, such as:
- Durability
- Incorporating failsafes
- Managing temperature
High-current PCBs must withstand heavier-than-average loads, which can be a challenge. Heavy copper used for these circuit boards is thicker compared to a PCB with more signals and lower power, which requires a rigorously controlled solder mask procedure. However, our team of experts has the knowledge and experience to complete the process to the highest standards.
To mitigate designs that may go awry, you can incorporate failsafe protection such as fuses or onboard thermal sensors. Failsafe fuses alleviate short circuits, while temperature sensors monitor hotspots and other crucial components. Temperature monitors help your PCB adjust to hotspots, making them a reliable way to monitor the board’s pulse.
Printed circuit boards can only handle a specific amount of heat, which depends on the materials used. If a PCB can withstand about 150 degrees Celsius, it meets the criteria for a high-temperature board. PCBs manufactured from materials with high heat resistance like Polyimide can sometimes withstand hotter temperatures, while those with less resistance can operate only at lower temperature levels.
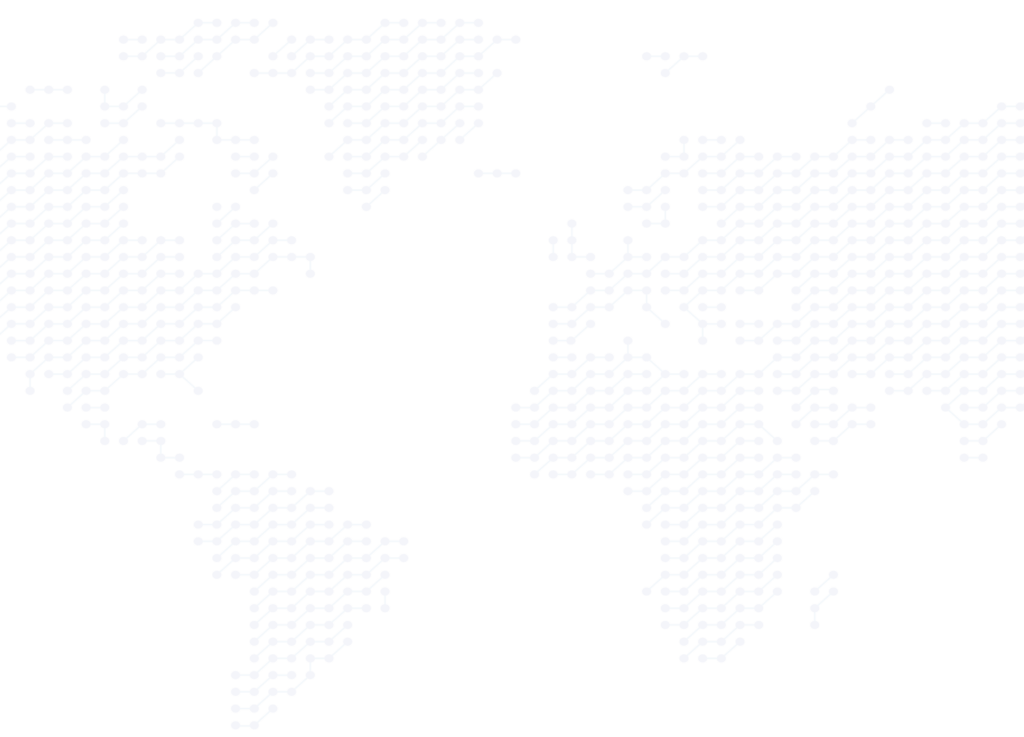
Get a Free Quick Quote.

Common High-Current PCB Applications
PCBs with a heavy copper base can take on high current loads to support applications such as:
- Automotive
- Aviation
- Heavy machinery
- Power converters
- Power supplies
- Solar arrays
- Transformers
- Welding
If your project demands higher currents, a compact board design and a durable circuitry connection, heavy copper PCBs are beneficial. Even under high temperatures, these boards won’t disrupt or warp. Industrial equipment that uses high-current PCBs powers some of the most innovative technologies.
Many industries require PCBs to tolerate high voltage. However, some applications that don’t initially use high currents still need a PCB because of unfavorable conditions like low air pressure causing voltages to arc faster.
Because of advanced materials, the demand for PCB designs and circuit board manufacturing capabilities, PCB applications are rising. Today, they’re surpassing simple solutions and more industries are becoming part of the high-circuit PCB world.
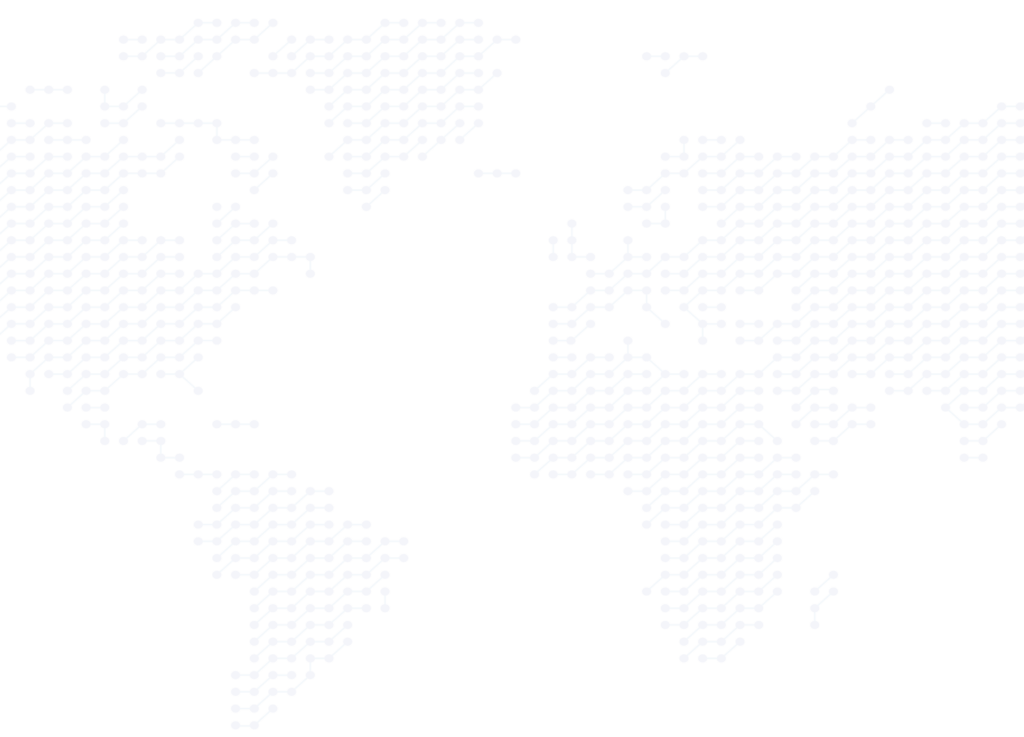
Our Capabilities for High-Current PCB Applications
Thick copper traces from Millennium Circuits Limited allow for more thermal resistance and can handle higher current rates. Our solutions can also withstand higher temperatures for extended periods for stronger connection points. With a heavy copper PCB, you can opt for single- or double-sided solutions or ones with multiple layers.
The first two options are simple configuration design options, while the multilayer board is more complex. Multilayer PCBs can relay heavy current loads while simultaneously handling multiple functions. Copper traces like these support industries that require higher processes and performance levels.
Millennium Circuits Limited manufactures heavy copper PCBs with copper weight from 3 oz./ft² to 10 oz./ft². If you need more than 10 oz./ft², we can still support your requests.
Browse Our High-Quality PCBs Today
At Millennium Circuits Limited, our expertise in high-current PCBs will support your business success. We offer top-tier printed circuit board solutions at competitive prices. Our team of experts also delivers dedicated support services and works with you in understanding our innovative PCB solutions.
Reach out to a Millennium Circuits Limited representative if you have questions or browse our high-current printed circuit boards online.
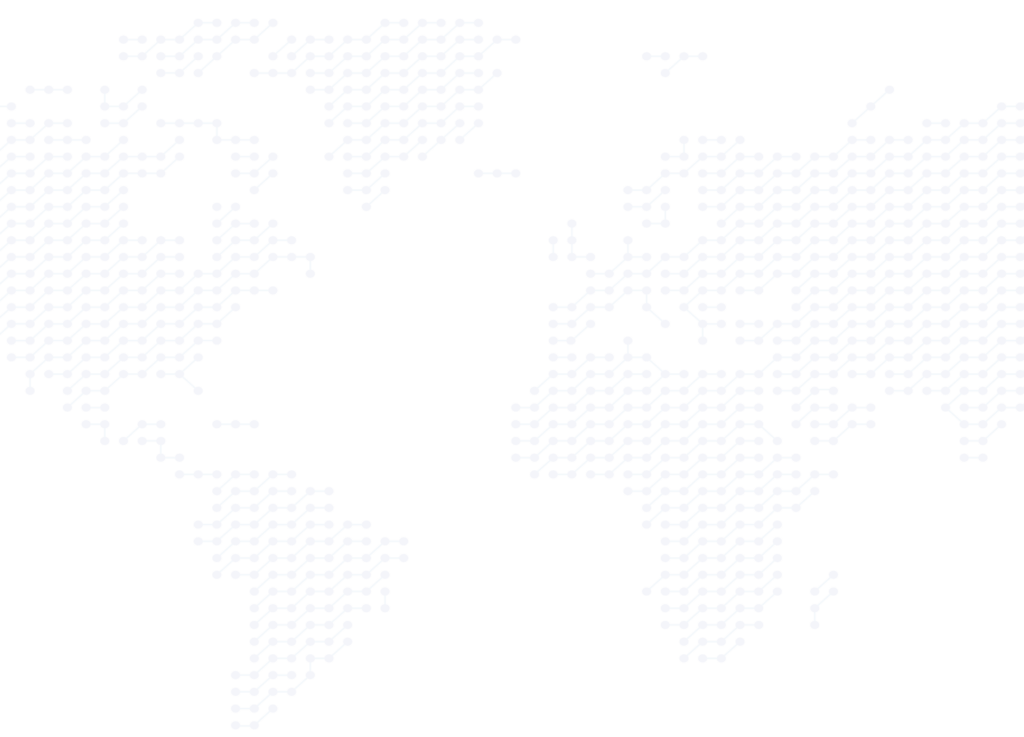