PCBS for Railway Applications
Modern railway systems are at the forefront of delivering rapid, secure, and sustainable transportation solutions, aligning with the demands of our era. While we acknowledge certain challenges in this domain, such as ensuring seamless passenger connectivity and enhancing comfort, as well as boosting line capacity, we remain committed to addressing these issues proactively.
In pursuit of our dedication to innovation and progress in railway transportation, we are pleased to present a selection of applications we offer, all aimed at elevating the passenger experience and expanding the capacity of these vital transportation networks.
- Braking Systems: PCBs for all different parts of the braking systems: monitoring communication, temperature and brake pad wear warning system. Demands are DIN EN 50155/IEC 60751 and controlled smoke development/material choice in case of fire. Crucial factors are high reliability, size constraints, redundancy and harsh conditions.
- Pantograph Systems: PCBs for high voltage power conversion, Insulation Gate Bipolar Transistor (IGBT). Demands are DIN EN 50155/IEC 60751. Crucial factors are high reliability and harsh conditions.
- Propulsion: PCBs for motor control/drive electronics, high voltage power stages and control units. Demands are DIN EN 50155/IEC 60751 and controlled smoke development/material choice in case of fire.
- Signal Systems: PCBs for the railway track, control center and trainset. Applications like switches, balun units, communication control, lightning protection, voltage control and GPS plus equipment within the trainset. Demands are DIN EN 50129. Crucial factors are backup safety, rugged construction, long lifespan and no downtime.
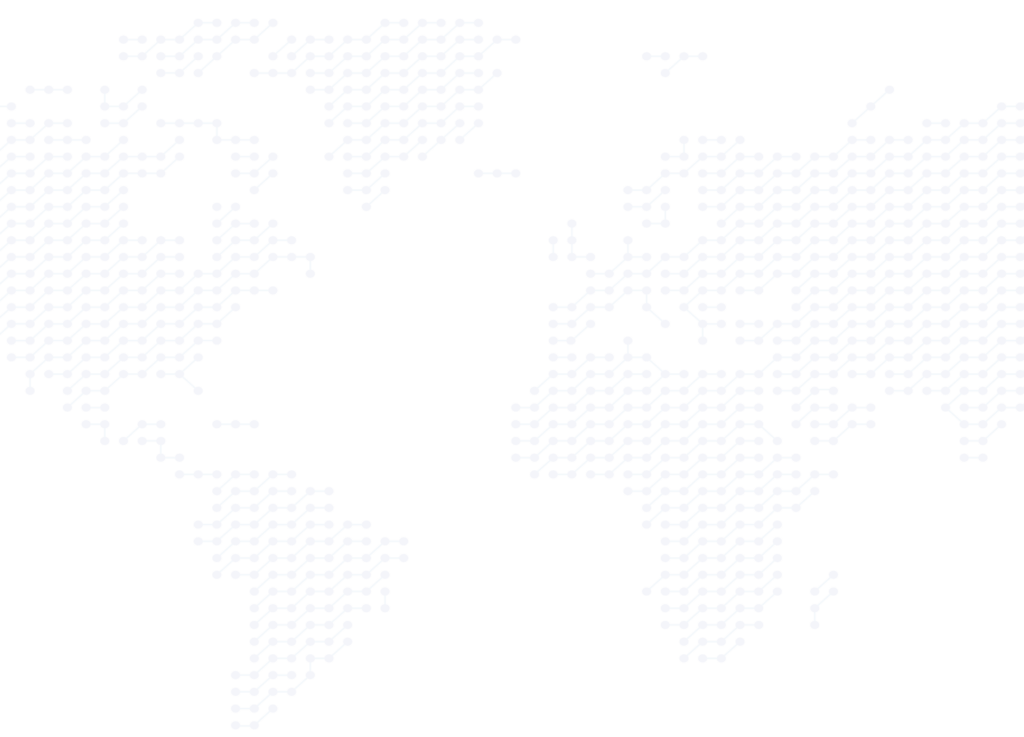
Challenges of PCBS for Railways
PCBs are integral components in the railway industry, playing a crucial role in the operation, control, and safety of railway systems. These boards facilitate the complex electrical connections required for various railway applications, including signaling, communication, traction control, onboard systems, and monitoring devices.
In railway signaling systems, PCBs are used in control panels, signal processing units, and trackside equipment to ensure the safe and efficient movement of trains. They enable the transmission of signals between track circuits, switches, and signals, allowing for the precise control of train movements and the detection of potential hazards on the track.
Communication systems onboard trains rely on PCBs for the integration of radio transceivers, antennas, and communication interfaces. These boards enable wireless communication between trains, control centers, and signaling infrastructure, facilitating real-time data exchange for operational monitoring, passenger information systems, and emergency communications.
Moreover, PCBs are vital components in traction control systems, which regulate the power delivery to locomotives and electric multiple units (EMUs). These boards interface with propulsion systems, motor controllers, and power converters to optimize energy efficiency, traction performance, and braking functions, ensuring smooth acceleration, deceleration, and speed control of trains.
In addition to operational systems, PCBs are essential in onboard monitoring and diagnostic equipment, such as condition monitoring systems, event recorders, and surveillance cameras. These boards enable the collection, processing, and transmission of data related to train performance, track conditions, and safety-critical parameters, allowing railway operators to monitor equipment health, detect faults, and improve maintenance practices.
The design and manufacturing of PCBs for the railway industry adhere to stringent standards and regulations, including safety, reliability, and electromagnetic compatibility (EMC) requirements. Robust designs, high-quality materials, and rigorous testing procedures are employed to ensure the durability, resilience, and long-term performance of PCBs in railway applications.
Overall, printed circuit boards are essential components in the railway industry, contributing to the safety, efficiency, and reliability of railway systems worldwide. They enable the seamless operation of signaling, communication, traction control, and monitoring systems, ensuring the smooth and secure movement of trains and passengers along railway networks.
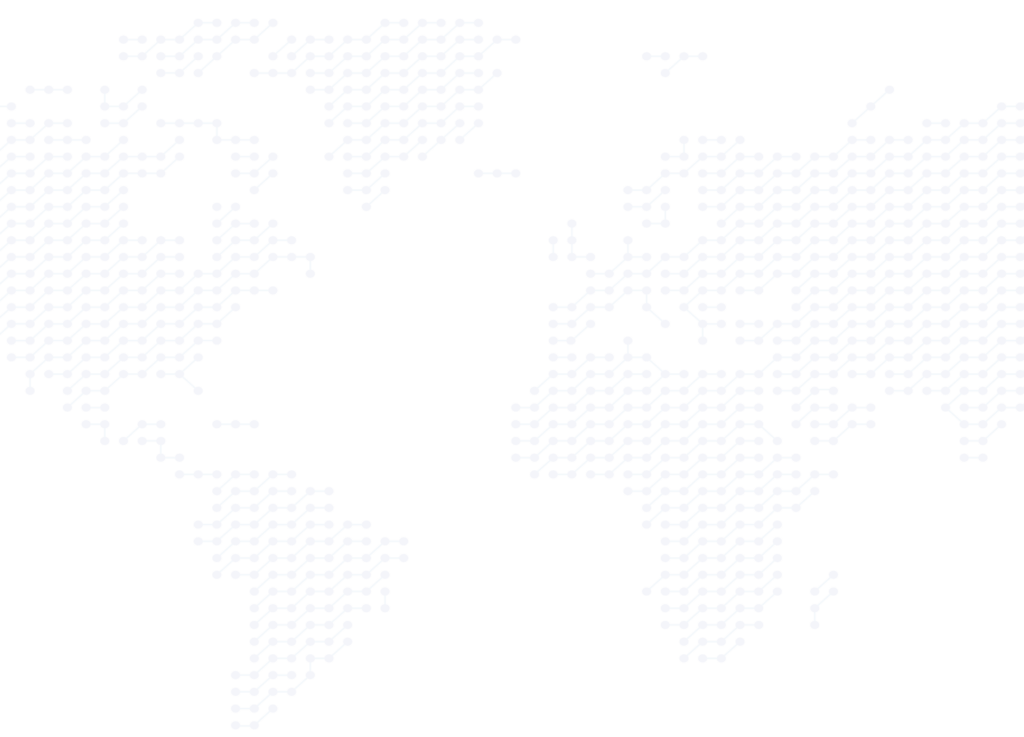
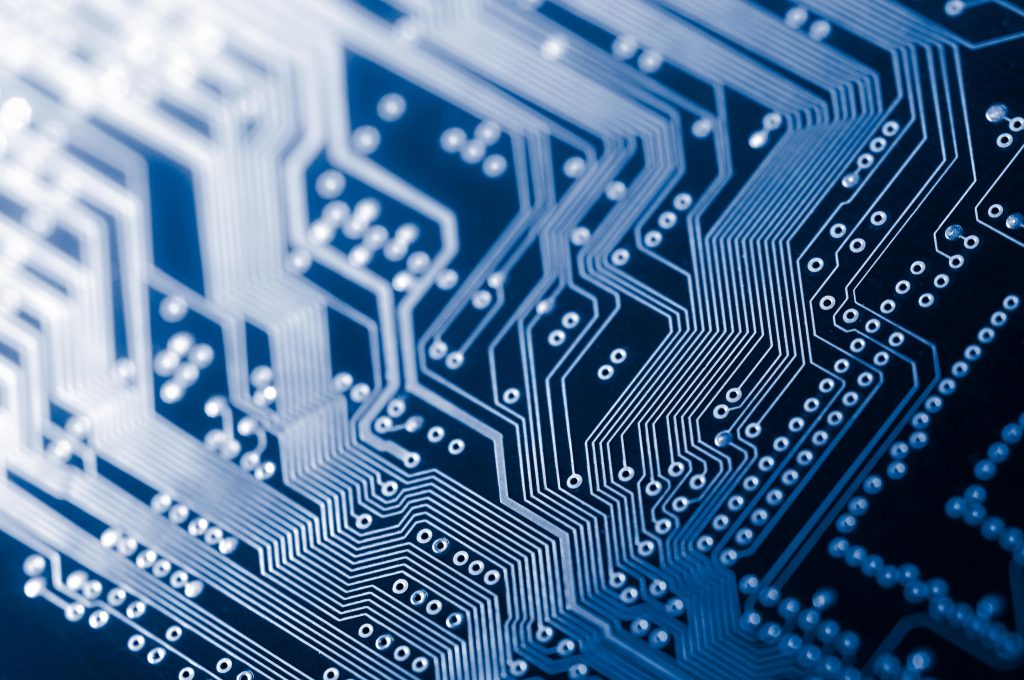
Designing PCBS for Railway
Designing Printed Circuit Boards (PCBs) for railway applications involves adhering to specific standards and considerations to ensure safety, reliability, and performance in the challenging environments these systems operate in. Here’s a comprehensive overview of the design considerations for PCBs in the railway industry, based on the established website copy and additional information sourced from relevant standards and guidelines.
Key Standards and Regulations
- IEC 61508 and CENELEC Standards: The design and manufacturing of PCBs for railway applications must comply with international and European standards for safety and reliability. IEC 61508 provides guidelines for the functional safety of electrical, electronic, and programmable electronic systems, emphasizing the importance of safety management from the initial stages of design. CENELEC standards, particularly EN 50126, EN 50128, and EN 50129, focus on safety management, software management, and system safety of electronic railway equipment.
- EN 45545-2 for Fire Safety: PCBs used in railway applications must also meet stringent fire safety requirements to protect against fire hazards. EN 45545-2 specifies the requirements for fire behavior of materials and components in railway environments. This includes tests for smoke density and toxicity, ensuring that materials used in PCBs minimize the risk and impact of fires.
Design Considerations
- High Reliability and Harsh Conditions: PCBs must be designed for high reliability under harsh operating conditions, including vibrations, temperature extremes, and mechanical stresses. This is critical for systems such as braking, propulsion, signal systems, and onboard datacom systems.
- Safety and Redundancy: Backup safety features and redundancy are crucial for systems like signal systems that play a vital role in the safe operation of railway services. Ensuring long lifespans and minimal downtime is also a priority.
- Controlled Smoke Development and Material Choice: When selecting materials for PCBs, considerations include controlled smoke development and the choice of materials that do not propagate fire. This is particularly important for braking systems and propulsion units.
- Multilayer PCBs and HDI (High Density Interconnect): The complexity of railway systems often requires the use of multilayer PCBs and HDI technology to accommodate the circuitry needed for advanced functionalities such as high-speed data transmission and power conversion.
- Compliance with Specific Technical Standards: Applications such as pantograph systems for high voltage power conversion and onboard climate control systems must adhere to specific technical standards, including DIN EN 50155/IEC 60751 for general railway applications and TB/T 3139-2021, SN30412-1 (002) for certain advanced functionalities.
Designing PCBs for railway applications demands a comprehensive understanding of the specific regulatory environment and technical challenges. Compliance with safety standards, fire regulations, and the careful selection of materials and PCB technologies are all critical to ensuring the reliability, safety, and performance of railway systems. By incorporating these considerations from the outset, designers can ensure their PCBs meet the stringent requirements of the railway industry, thereby contributing to safer and more efficient railway operations.
Contact us for a free quick quote.

Exploring the Benefits of High Current Heavy Copper PCBS
When it comes to printed circuit boards (PCBs), high current PCBs, also known as heavy copper PCBs, offer invaluable advantages. At MCL, we supply heavy copper PCBs ranging from 3 to 10 oz/ft2, with options for extreme copper concentrations. Here’s why you should consider them:
- Robust Structure: Heavy copper enables higher density and fewer layers, resulting in a simpler yet stronger structure, perfect for demanding applications like connectors.
- Reduced Failure Rate: These PCBs efficiently dissipate heat, minimizing the risk of failure even under high currents and temperature fluctuations.
- Cost-Effective Production: Despite slightly higher material costs, heavy copper PCBs offer overall production savings. They can replace copper cables and integrate seamlessly with standard features, reducing layers and production costs.
Experience the reliability and efficiency of high current heavy copper PCBs with MCL today.
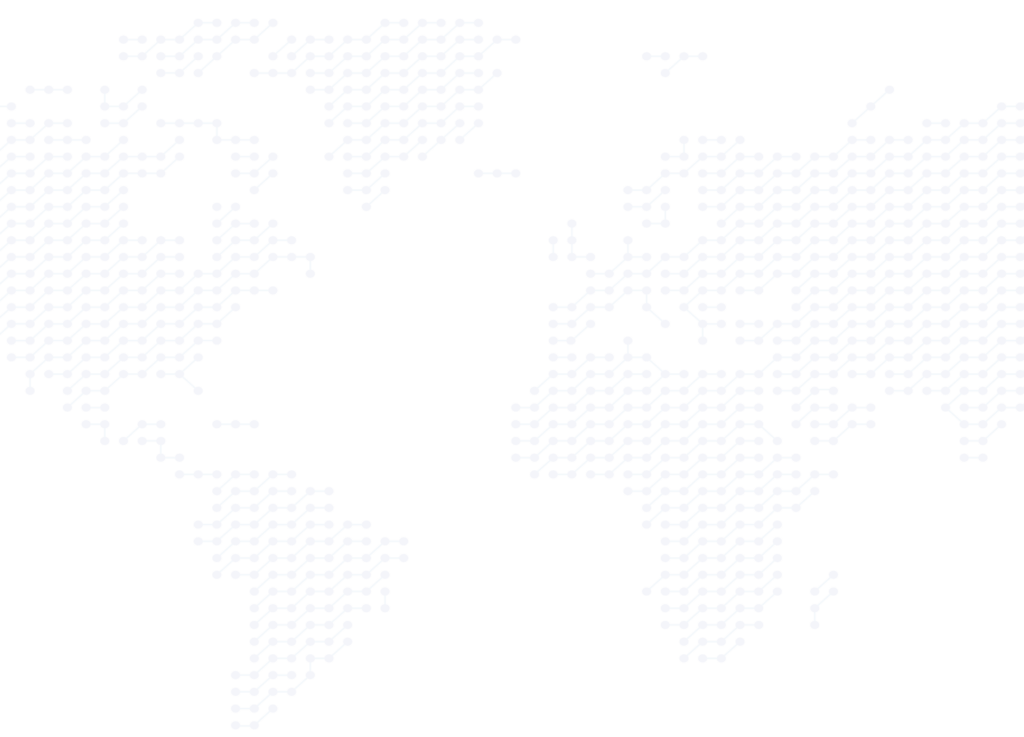